 |
您目前的位置:首页--企业黄页 |
|
四川达州钢铁集团公司已形成年产铁350万吨、钢350万吨、钢材350万吨、冶金焦炭210万吨的规模。在这些产品生产过程中,产生了可再次利用的高炉煤气、转炉煤气、焦炉煤气和富态的蒸汽。为实现能源的循环利用,该公司推行了分布式能源技术的应用,为企业带来了经济效益,也取得了良好的社会效益。
分布式能源技术具有能源利用效率高、环境负面影响小、提高能源供应可靠性和经济效益好的特点,成为了供能发展趋势的重要方向之一。首先,安全稳定性高。分布式能源在传统供电、供热、供冷之外,在供能方式上提高双重保障,使运行系统更加安全稳定;其次,节能能耗优势显著。分布式能源以“温度对口,梯级利用”为原则,大大提高能源利用效率,把损耗降到最低;再其次,减少碳排放。分布式能源与传统常规系统相比,C02减排量达50%,SO2和固体废弃物排放几乎为零,减少NOx排放量达80%。
分布式能源技术的基础科学主要在以下几个方面:其一,动力与能源转换设备:主要是指一些基于传统技术的完善和新技术的发展;其二,一次和二次能源相关技术;其三,智能控制与群控优化技术;其四,综合系统优化技术;其五,资源深度利用技术。达钢依据企业实际,在分布式能源技术的应用上,主要通过以下十个方面来实现的:第一,充分利用钢铁行业多种煤气资源,依托设计科研单位开发生产石油替代产品二甲醚。该公司实施了以焦炉煤气、转炉煤气生产甲醇和二甲醚工程,投资达9.7亿元。
据悉,该项技术已被受理专利申请,并且经国家发改委组织专家验收,核定年节能约19.35万吨标煤,同时获得国家财政奖励资金4837.5万元。
第二,回收利用高炉煤气,推行热电联产。随着高炉炼铁的发展,该公司先后实施了高炉煤气综合利用发电一期和二期工程,先后建成了12兆瓦抽汽凝汽式和15兆瓦凝汽式发电机组各一套,年利用富余高炉煤气10亿立方米以上,年可供出电能1.8亿千瓦时左右、提供1兆帕蒸汽30万吨左右,同时替代淘汰了20吨/小时燃煤工业锅炉3台,年节能9.3万吨标煤,创造价值约9000万元。
第三,新建高炉炉顶煤气余压发电(TRT)工程回收煤气余压、余热。该公司对两座高炉建设一套两炉一机TRT发电机组,在同行业中属较早使用此项技术,年可供出电能2200万千瓦时左右,年节能约7700吨标煤,创造价值约3000万元,同时有效地降低了区域噪声,改善了职工工作环境。
第四,转炉煤气回收利用节能技改工程。该工程从2007年开始实施,于2008年3月竣工投产,使原放散的转炉煤气得以回收利用,现转炉系统煤气回收量已达到约90立方米/吨以上,实现年节约能源约4000吨标煤以上。
第五,新建饱和蒸汽余热发电工程回收利用蒸汽余热。在炼钢、轧钢余热蒸汽回收利用项目基础上,为充分利用低温蒸汽的余热余能,该公司投资5036万元实施了饱和蒸汽余热发电项目,该项目于2011年8月竣工投产后,使转炉蒸汽回收利用量达到90千克/吨以上,年发电量6400万千瓦时,年节能1.94万吨标煤。
第六,新建烧结余热发电工程回收利用烧结废气显热。为了充分利用烧结机废气显热,该公司投资8000余万元实施了烧结余热发电项目,该项目于2012年初竣工投产,年发电量9360万千瓦时,年节能2.7万吨标煤、减少S02排放198吨。
第七,采用先进工艺技术和设备对新厂区捣固焦炉实施干熄焦余热发电节能技改项目。该项目总投资1.8亿元,已于2011年11月竣工投产,年产蒸汽554880吨,年节能3.8万吨标煤。
第八,采用先进工艺技术和设备对老厂区3座机械化焦炉实施干熄焦余热发电节能技改项目。该项目总投资1.6亿元,于2012年4月竣工投产,年发电12917万千瓦时,年节能2.4万吨标煤。
第[FS:PAGE]九,为了改善厂区环境,减少SO2排放,该公司于2009年~2010年投资5500余万元实施了1号烧结脱硫项目和2号烧结脱硫项目,并先后于2010年3月和11月竣工投产。两个项目的实施使脱硫系统平均脱硫效率为90.27%,投运率为92.4%,综合脱硫效率为83.41%,年减少S02排放4000余吨,具有十分显著的环保效益。
第十,推行焦炉烟道气余热利用技术。该公司投资2000万元对新、老厂区焦炉的烟道气进行技术改造。目前该项工作中正在进行中,预计改造完工后,年产蒸汽21万吨,年节约标煤1.44万吨标煤。
今年以来,达钢在分布式能源技术的应用上取得了初步成效。接下来,该公司将对能源综合利用和深度开发方面进一步深入研究,力求最大限度地实现稳定、安全、高效的能源梯级利用,不断探索劣质能源资源回收再利用,推进节能减排工作不断深入。( 责任编辑:管理员 ) |
|
|
|
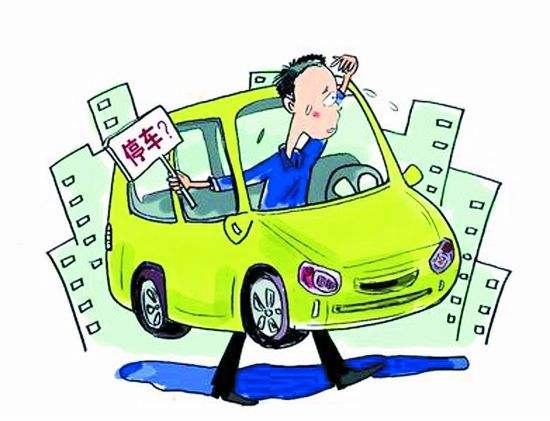 |
|
因地施策,破解停车难 |
|
|
|
|
|