 |
您目前的位置:首页--合同能源 |
|
时间:2012-3-15 来源:中国合同能源管理网 |
“十一五”以来,成本低、收效快的常规节能降耗技术在胜利油田已得到广泛应用,留下的节能空间日益变小,节能降耗的潜力在哪里?中石化胜利油田深挖潜力,积极引入合同能源管理,着力推动循环经济,用取得的突出成绩给出了答案。
合同能源管理效果初显
2009年以来,胜利油田现河采油厂没花钱买新设备,却对200口油井进行了节能设备改造,200口油井平均综合节电率达25%以上,年节电300余万千瓦时。这是该厂应用合同能源管理取得的节能成果。
现河采油厂应用合同能源管理最大效果就是“合作共赢”。该厂实行合同能源管理过程中,甲乙双方收益共享,风险共担,与从前花钱买设备相比,确保了节能项目的实效。由厂家提供设备及配套技术,达不到电量和单耗下降的目的,作为甲方的采油厂不承担任何费用。同时,设备的安装维护均由厂家负责,提高了设备利用率。倘若设备出现问题,厂家第一时间维护,争取了时间,把对生产的影响降到最低。最为关键的是,这样不仅节能,而且节省资金。
由于设备配套合理了,油井参数优化了,不仅产油量没有受到影响,而且使皮带寿命延长,设备磨损降低,作业频次明显减少。采油站上的职工对此评价是:活干得少了,钱拿得多了。如今,合同能源管理正在被现河采油厂越来越多的下属单位所接受。
循环经济推动节能减排
面对成本不断增加、缺少规模效益的现状,胜利油田石化总厂通过走低能耗、高效率的循环经济模式持续推动降本减排,取得了较好的经济效益。2011年,该厂综合能耗降到80.5千克标油/吨,创历史最好成绩。该厂把生产过程中产生的大量废物,由“包袱”变成了企业发展的财富,实现了资源循环利用和产业良性互动。
在“油”上想办法。“现在我们的加热炉已经不烧燃料油了,取而代之的是装置产生的瓦斯气,每月可节省燃料油1000多吨。”石化总厂焦化车间主任张海莹说。针对生产一方面需要大量燃料油,另一方面瓦斯气白白浪费的现状,该车间开展了回收利用攻关,建成了万方气柜回收装置,通过制订多部门瓦斯协调方案,鼓励多烧瓦斯少用油。现在常减压、动力、延迟焦化等主要装置的瓦斯气利用率明显提高,原来火炬烧掉的瓦斯气被用来替代燃料油,每年节省燃料油10960多吨。
在“水”上做文章。为了更合理地回收利用再生水源,石化总厂开发出一种特性陶瓷膜管对凝结水进行除油除铁。经装置处理后出来的凝结水直接可以作为锅炉补水。2009年以来,该装置已处理凝结水15万吨。该厂还通过实施东生化池增设沉降段、增加外排污水回用等10多项工艺和设备改造,使外排水合格率能够保持在96%以上,达到国家工业污水二类二级排放标准,部分指标达到一级标准。
在“汽”上下功夫。“工业风管网虽然都加了蒸汽保温,但是我们每次放空都要等蒸汽排出后再关闭放空阀,这样就节约了蒸汽。”负责工业风管网维护的空分车间职工郭宣斌说。焦化车间针对重油管线较多,伴热线较多的实际,岗位职工群策群力,进行降低装置伴热蒸汽用量的攻关。成果实施后,每年可节约蒸汽2万吨。( 责任编辑:管理员 ) |
|
|
|
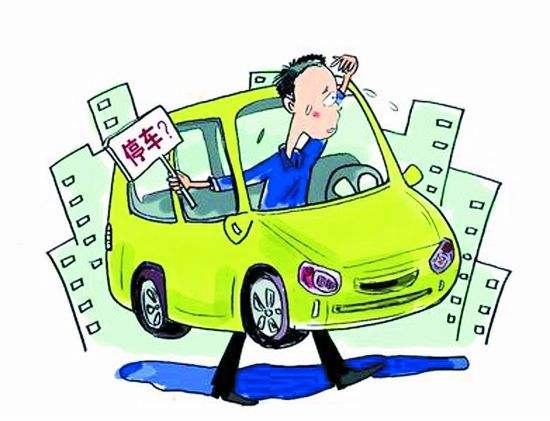 |
|
因地施策,破解停车难 |
|
|
|
|
|