 |
您目前的位置:首页--成功展示 |
|
浙江华东铝业有限公司的技术人员向记者介绍了该公司国内率先成功应用的新型阴极结构电解槽技术。此项技术集中了铝液和火焰焙烧的优点,不仅提高了电解槽的焙烧质量,而且大大缩短了焙烧时间,降低了能耗和焙烧费用,节能效果显著。
浙江华东铝业有限公司的技术人员向记者介绍了该公司国内率先成功应用的新型阴极结构电解槽技术。此项技术集中了铝液和火焰焙烧的优点,不仅提高了电解槽的焙烧质量,而且大大缩短了焙烧时间,降低了能耗和焙烧费用,节能效果显著。
“该技术的成功应用,将为公司实现节能降耗、促进效益增长发挥积极作用。”该技术人员说,目前,该公司200千安培系列电解槽已改造完毕,按吨铝节电1000千瓦时计,可年节电5000万千瓦时,相当于年节省标煤1.75万吨,可减少二氧化碳气体排放量5万多吨。
华铝公司是华东地区最大的有色金属冶炼加工企业之一,也是我省唯一属于国家允许和鼓励类的电解铝生产企业。目前,公司为中国有色金属行业50强重点企业,具备12万吨电解铝的生产及加工能力。
近20年来,国内外铝电解生产技术有了很大进步,但工业电解铝生产大幅度节能减排技术一直是铝行业的重点攻关目标。众所周知,浙江是一个缺煤少电的省份。为此,华铝公司苦练“内功”,立足节能降耗和降低成本,着力做好降低电耗这篇文章,通过淘汰自焙槽、自动定点加料、降低阳极效应,并采取延长槽龄、铝电解综合节电等技术措施,节能降耗效果显现。
然而,要进一步降低电耗,仅仅依靠目前的管理水平及技术条件,很难再上一个新台阶,必须在技术上有新的突破,工艺上有新的创新。2007年,东北大学发明了一种新型阴极结构的铝电解槽,可使电解槽工作电压从4.1伏降低到3.75~3.78伏。与目前电解槽相比,吨铝电耗可降低1000千瓦时左右。可以说,此项技术是铝电解发展史上的一次重大技术革命和极具推广意义的创新,为世界首创、具有我国自主知识产权和核心技术。
2008年下半年,由于金融危机影响,铝价直线下滑,进一步降低铝电解电耗时不我待。为确保实施该技术,华铝公司成立项目实施领导小组,通过科学论证,决定将已服役6年的200千安培电解槽系列停产大修,采用新型阴极高效节能电解槽技术,将现行的200千安培、240千安培铝电解系统,结合电解槽大修进行节能改造和技术升级,并且采用与该技术相配套的铝电解槽火焰———铝液二段焙烧新工艺和相对应的电解操作技术,使通电焙烧时间缩短一半,单槽通电焙烧费用比原先节约数万元,达到了高效节能的目的。
新型阴极结构电解槽技术的成功应用,使华铝公司实现生产成本大“瘦身”。目前,该公司200千安培新型阴极系列电解槽通过几个月的运行,已充分显示出其技术先进性和节能降耗效益。从运行的两种电解槽能耗、产量相比,新型阴极电解槽吨铝节电可达1000千瓦时以上,节电8%左右。
该公司有关负责人说:“200千安培和240千安培新型阴极系列电解槽改造项目完成后,每年可节电1.2亿千瓦时,相当于节约标准煤4.2万吨。”( 责任编辑:管理员 ) |
|
|
|
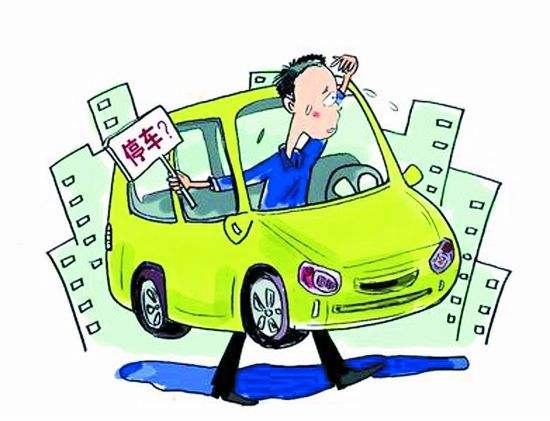 |
|
因地施策,破解停车难 |
|
|
|
|
|